“I wish I could invent something like blue jeans. Something to be remembered for.” –Andy Warhol
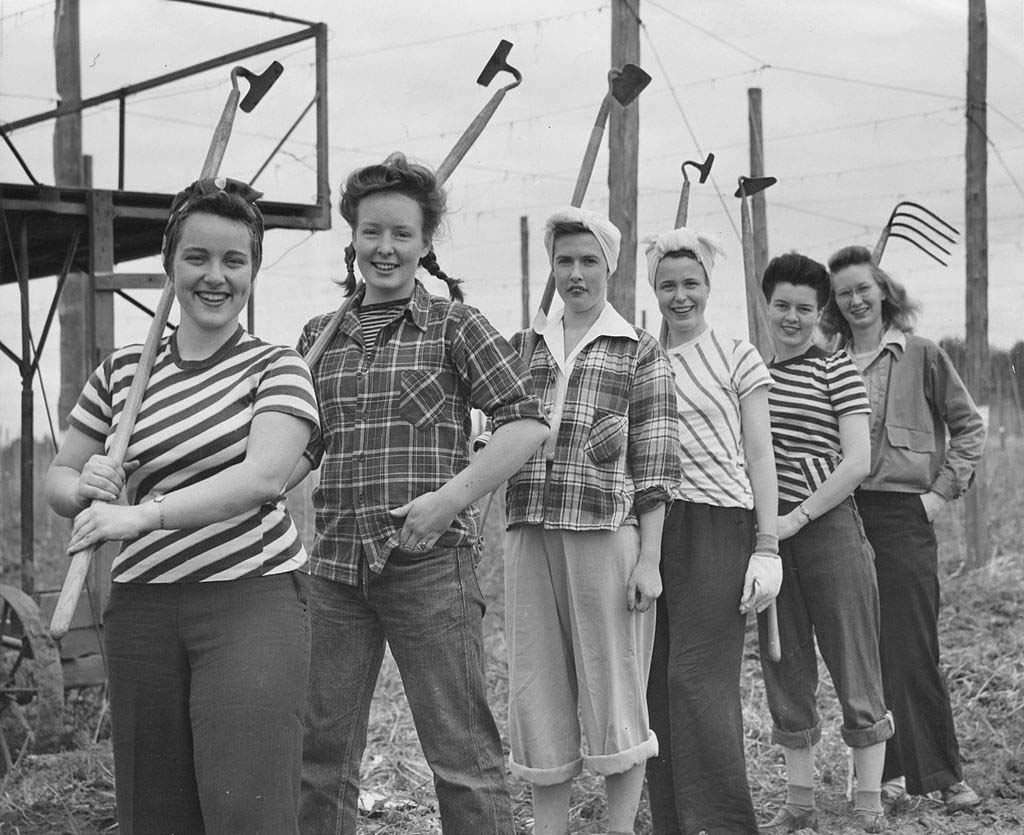
“I have often said that I wish I had invented blue jeans: the most spectacular, the most practical, the most relaxed, and nonchalant. They have expression, modesty, sex appeal, simplicity - all I hope for in my clothes.” –Yves St. Laurent
Denim is the most democratic of materials. It is also the fabric of America. No other fiber has come to more closely represent the ideals, vision, and spirit of the “Land of the Free.” And I’m saying this as a Canadian; you guys really nailed this one. Americans invented attitude. That attitude is the color of indigo and has a history so rich and compelling it has spawned books, Elton John songs, protest movements, advertising revolutions.... and acid wash.
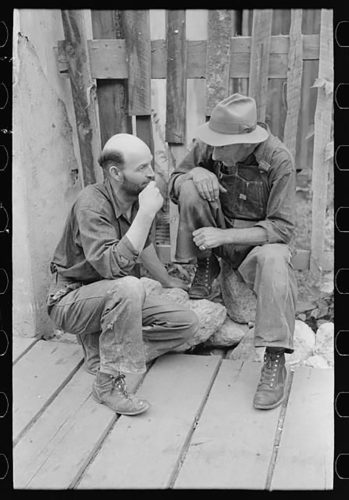
Jeans were built to withstand the backbreaking
labor involved in gold mining.
If I may be so bold, I would argue that denim built America––at least large swaths of it. It mined the West, roped the cattle, oiled the machines, and built the cars that made the country what it is. Denim was the armor that protected vulnerable human bodies from the wonder and danger inherent in progress. And when it was done building the backbone of America, it built its culture. It was, and is, the uniform of rebellion, rock and roll, social change, sex, youth, revolution, and independence.
While denim has since become emblematic of a national identity and way of life, it had ever-so-humble beginnings. During the Gold Rush in the nineteenth century, an enterprising immigrant by the name of Levi Strauss saw the need for durable, strong workwear that could withstand the backbreaking labor of gold mining. He began manufacturing heavy canvas overalls and pants, strengthened with metal rivets at points of stress. Strauss imported a durable twill fabric from France that was dyed with indigo, called serge de Nîmes. He invented Levi’s 501s in 1890, and the bottom half of America was never the same.
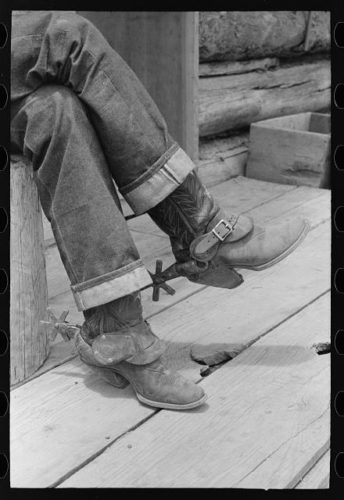
It is hard to imagine the west without it's
iconic denim.
After the Gold Rush, denim became emblematic of the West. It was the get-up of cowboys and ranch hands, later imported to the east coast in the 1930s by wealthy tourists, who were seduced by the romanticism of the dusty working class. It was made chic in the 1940s by Claire McCardell, the first American ready-to-wear designer of the twentieth century. Her designs were simple, modern, and functional. Denim was one of her preferred mediums, especially at a time of rationing during the war years. She helped usher denim into the wardrobes of busy, urban, American women.
While denim fabric may have started infiltrating the everyday wardrobes of middle-class women, jeans were another matter entirely. In the early 1950s, jeans were still the attire of the blue collar and the poor––until the birth of the teenager. America’s youth discovered itself in the later half of the decade; to the horror of parents, that discovery also included Chuck Berry, Elvis Presley, James Dean, and Marlon Brando. Blue jeans and rock and roll went hand in hand, and wearing a pair of 501s on a Friday night symbolized rebellion, nonconformity, and freedom from Bing Crosby, chinos, poodle skirts, and suburban Jello molds.
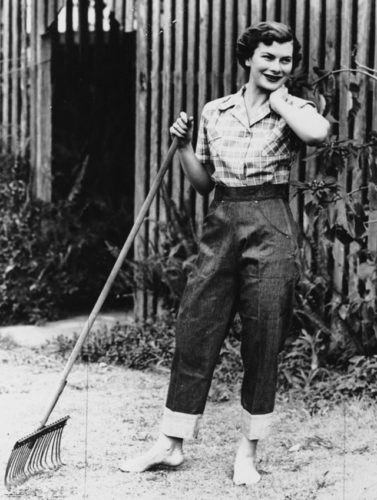
A young woman models her fashionable and
sensible denim in 1952.
By the 1960s, jeans had become the ne plus ultra wardrobe of youth culture. They bought them a size too big, so they’d shrink to fit, and then they wore them so tightly you needed pliers and a friend to help put them on. By the time the social protest movements and “Summer of Love “of the mid-60s shook America, jeans were the idiosyncratic uniform of the counterculture, personalized with beading, embroidery, and patches by long-haired men and women desperate to drop out of the mainstream and challenge the status quo. As Iain Finlayon writes in Denim: A Legend, “It was street fashion; it was ‘real life’ and ‘authentic’. It was, so far as possible, classless and anonymous, consciously and deliberately symbolic of a revolution that did not require clothes to symbolize position in a social hierarchy.”
In the 1970s, in order to dilute the rebellious power of jeans (like many threats to the nation’s security), they were absorbed and assimilated into the mainstream, made safe and boring through mass-market clothing and the Sears catalog.
But you can’t keep a good icon down; all it took was Brooke Shields going commando in Calvin Kleins to reassert their controversial spirit in the designer denim decade of the 1980s. From the Levi’s smuggled to European beatniks in the sixties, to Gloria Vanderbilt in the seventies, to the Naked & Famous brand today, jeans have always been a status symbol that advertise their worth on our best assets.
Since the invention of jeans in the nineteenth century, denim has been inextricably woven into the fabric of Western, post-industrial revolution culture. Although denim is most commonly known for its use in the production of jeans, it is a versatile and valuable fabric in any maker’s stash closet. Let’s see what makes denim so special.
“Blue denim is America’s gift to the world”. –Charles James
Denim Defined
The durability of denim comes from a combination of both the weave and fiber. Strong cotton thread is woven into a twill pattern, with more warp threads than weft. The vertical warp yarns are often indigo-dyed, while the horizontal weft yards are left white, producing the classic textured finish we equate with denim. Lighter-weight denims are generally a 2x1 twill, meaning there are two warp for every weft thread. Medium and heavyweight denim employ a 3x1 twill, with three warp threads creating an even more dense, resilient fabric.
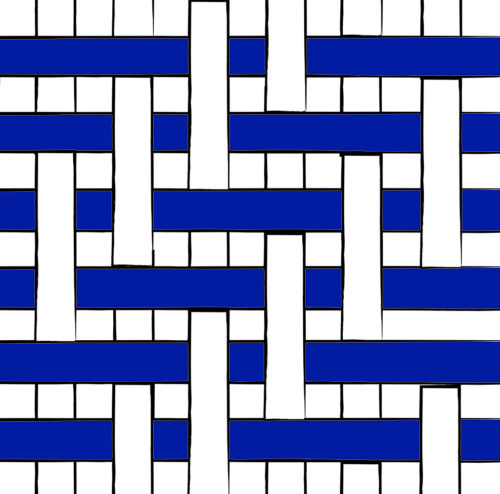
A traditional 2x1 weave
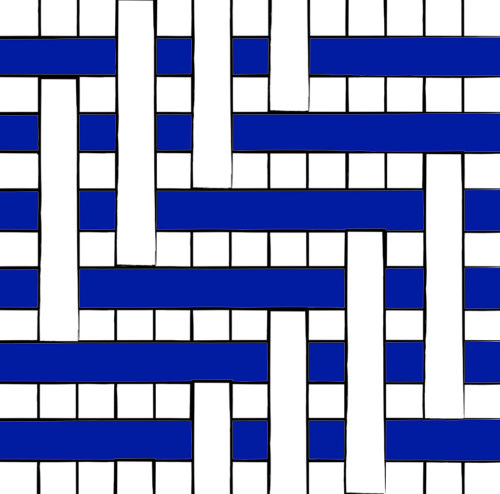
A traditional 3x1 weave
The twill train doesn’t stop there: 2x1 and 3x1 denim can further be broken down into left-hand, right-hand, and broken twill. Right-hand twill (RHT) has a diagonal pattern that travels from the bottom left to the top right of the fabric and is the denim you’re most likely to encounter; it shows strong fading and whisker lines from wear. Left-hand twill (LHT) is less common; it’s woven in the opposite direction of RHT and has a softer hand. Broken twill alternates at every two warp threads to create a zigzag pattern. If you’ve ever had an issue with leg twist in your jeans, understanding the fabric weave solves the mystery. RHT and LHT want to pull in the direction that they’re woven. While there are cutting strategies to deal with this problem, choosing a broken twill weave will eliminate twisting altogether since the fabric does not want to pull in one direction more than the other.
Finally, denim is measured in ounces by the square yard. Lightweight is technically anything under 12 oz.; a standard skinny jean is likely made with a 9–12 oz.denim, while jeggings are generally around 6–8 oz. Sturdy non-stretch jeans are made with heavyweight denim anywhere from 12–32 oz. Dresses and tops are best made with lightweight denim, unless you want something very structured. Anything over 18 oz. will be quite stiff and rigid, so it might be better left to décor sewing, unless you have your heart set on a pair of jeans that will stand up on their own.
Where Denim is Made
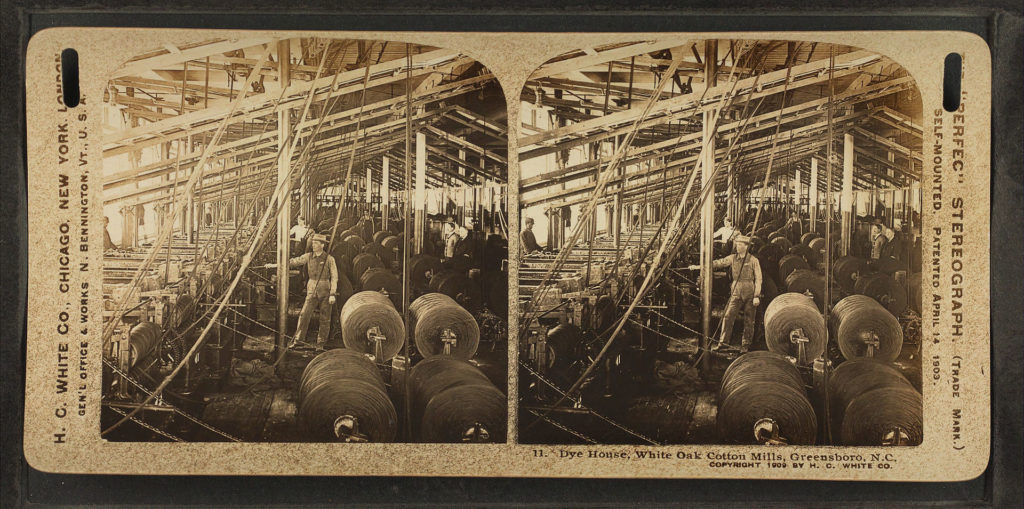
The dyehouse at the White Oak Cotton Mill in 1909. Photo credit: Courtesy of Cone Denim LLC, a division of International Textile Group.
While most of America’s mills have moved overseas, there are still a few companies making denim in the United States (US). The most notable is Cone Denim in Greensboro, North Carolina. They have been refining the denim making process since 1891 and are still manufacturing selvedge denim on some of the same looms they’ve owned and operated since the 1940s. A heritage company with generations of in-house experience, they are the supplier of choice for many designer jeans companies.
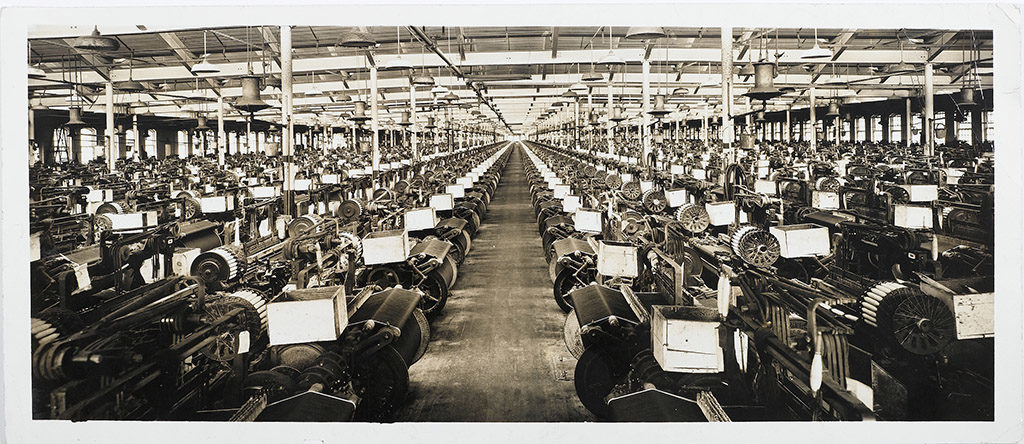
The Cone Denim weave room in 1941. Photo credit: Courtesy of Cone Denim LLC, a division of International Textile Group.
Japan is also renowned for its denim production, some companies using equipment they imported from the US when many great American mills were shutting their doors in the last century. Japan has a cult following among jean aficionados and is revered for its beautiful selvedge denim. Notable mills include Kurabo, Nisshinbo, Kaihara, and Kuroki.
Italy and Turkey also have a good reputation for quality mills, although they tend to focus more on innovative and fashion-forward denim. Reputable Turkish mills include Orta Anadolu and Isko. Italy is famous for Candiani and Legler. As a general rule, denim from Japan, the US, Italy, and Turkey, will be of a much higher standard and quality than denim milled in other countries, although there are always exceptions to the rule.
Loom Production
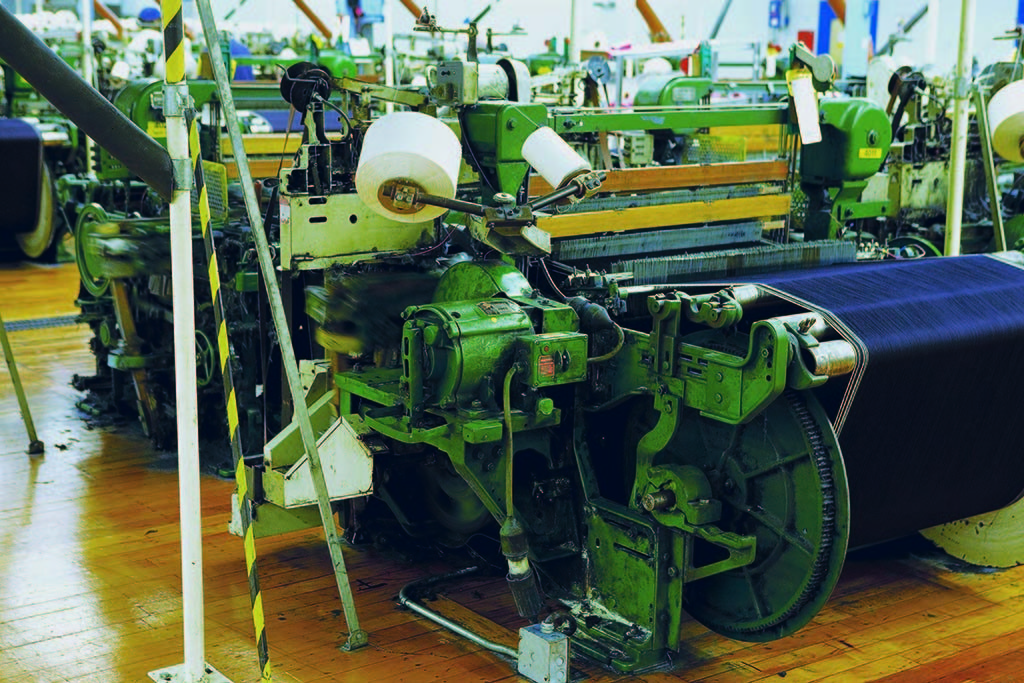
Shuttle looms create high quality denim with gorgeous texture and character. Photo credit: Courtesy of Cone Denim LLC, a division of International Textile Group.
There are two types of looms used to make denim. The shuttle loom was the first type of powered loom ever made. As such, it’s an older and slower technology, but this machine is responsible for the distinctive colored edge of selvedge denim. The edges of the fabric are finished, because the weft threads are continuously woven around the edge of the fabric. Shuttle looms can only produce 150 rows of weft yarn per minute, and as a result, are not as efficient as more modern looms. However, they create beautiful, high-quality denim with a unique texture and character.
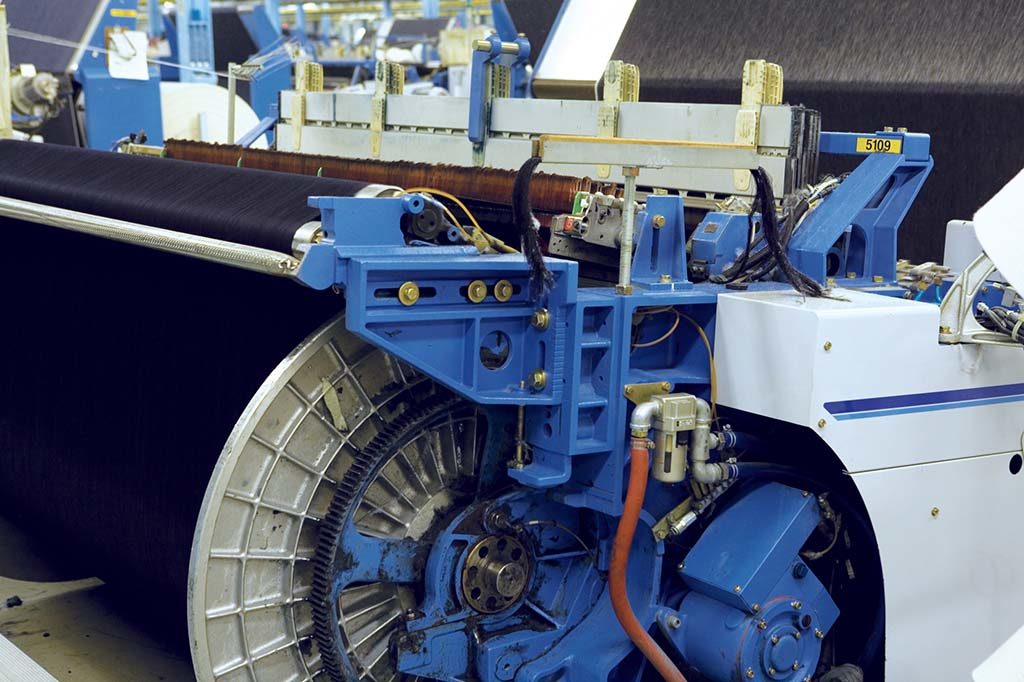
Though projectile looms offer the benefit of faster production, they do not yield the unique character of denim made from shuttle looms. Photo credit: Courtesy of Cone Denim LLC, a division of International Textile Group.
Projectile looms are a more modern technology. The main difference in production is that the weft yarn is not continually woven over each edge, resulting in a raw selvedge. They are up to eight times faster than a shuttle loom, and thus, highly efficient, although they cannot produce the trademark selvedge edge of the shuttle loom.
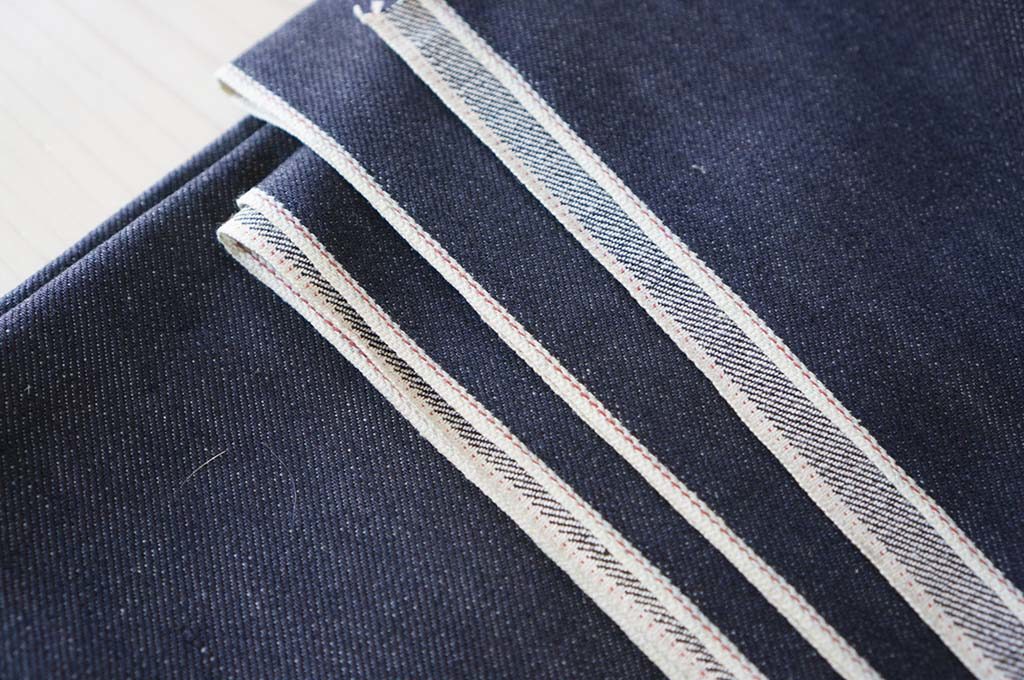
Selvedge denim features a selvedge that is finished rather than cut.
Denim Types
Selvedge
This type of denim comes in narrow widths (typically 30”) and has a finished selvedge, often with a decorative color like red or white woven in to the vertical edge. This detail is generally an indicator of high-quality denim. It’s often used in straight-legged jeans, since the selvedge edge does not need to be finished, and it creates a lovely construction detail.
Stretch Denim
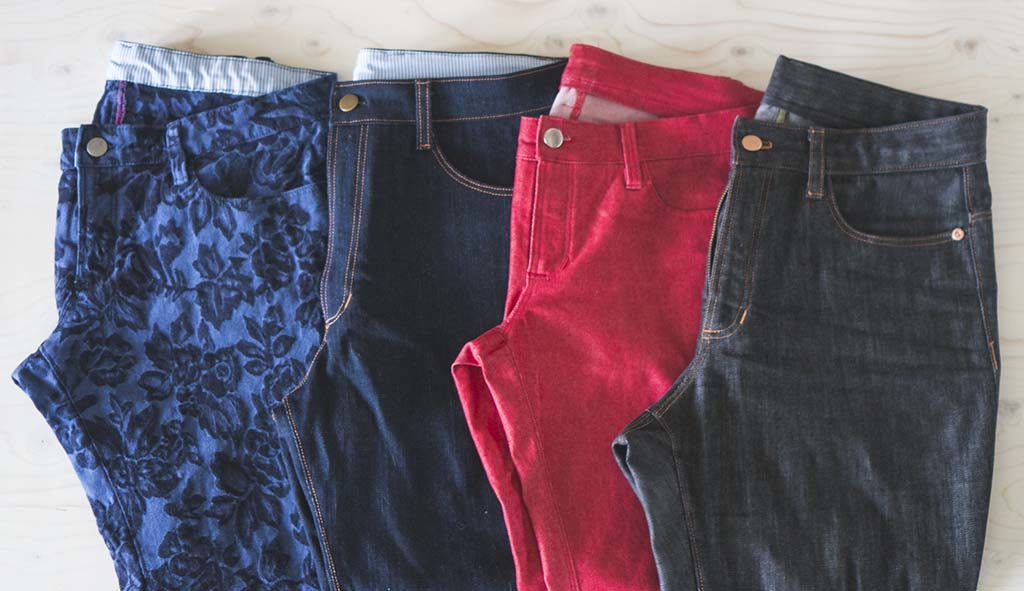
Stretch denim is a popular choice for skinny jeans.
In 1962, Cone manufactured the first stretch denim, making it possible to zip up high-waisted jeans without breaking a rib. Stretch denim is woven with a small percentage of Lycra, creating an elastic and forgiving fabric ideal for conforming to the curves of the female figure (and the fabric of choice for my Ginger Skinny Jeans pattern). It can vary greatly in quality, and the cheap stuff will “bag out” and lose its shape over time. Good quality stretch denim often blends a small quantity of polyester into the mix to help with recovery. It’s not always easy to determine the quality of stretch denim, especially online. When possible, buy from reputable sources or order swatches if you can. To test the recovery, give your denim a little pull and see how it snaps back. If it stretches out and doesn’t more or less return to its original state, it’s not likely to hold its shape on your body after being worn all day long.
Bull Denim
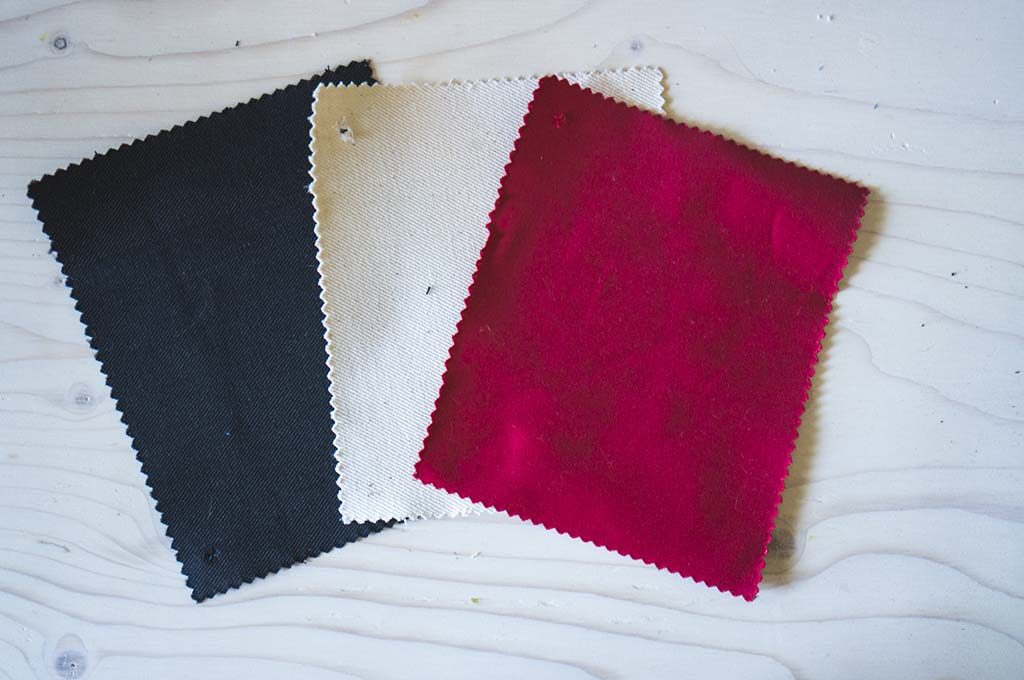
Any denim that has been dyed a solid color after it’s been woven is considered bull denim, but it can also be used to describe a rugged, heavyweight twill.
Shirting Denims
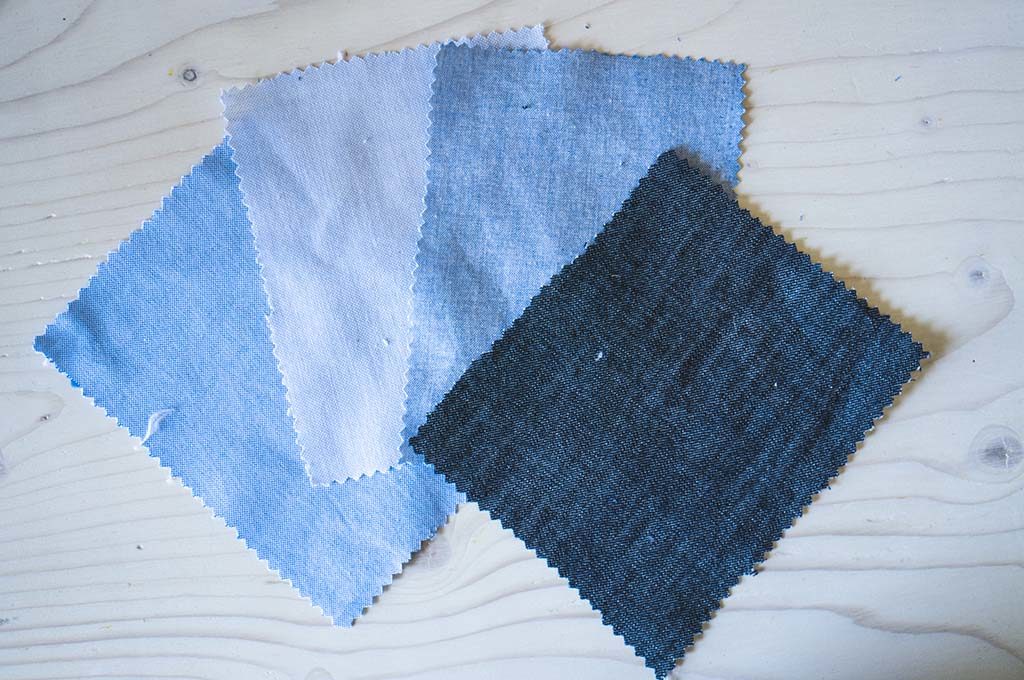
Chambrays have become a popular fabric choice for shirts and dresses alike.
Although not always appropriate for jeans, light-weight denims can make beautiful dresses and shirts. Although chambray is not true denim twill, it uses a similar weave of colored warp with a white weft thread and is often included in the denim section of fabric stores.
Novelty & Printed Denims
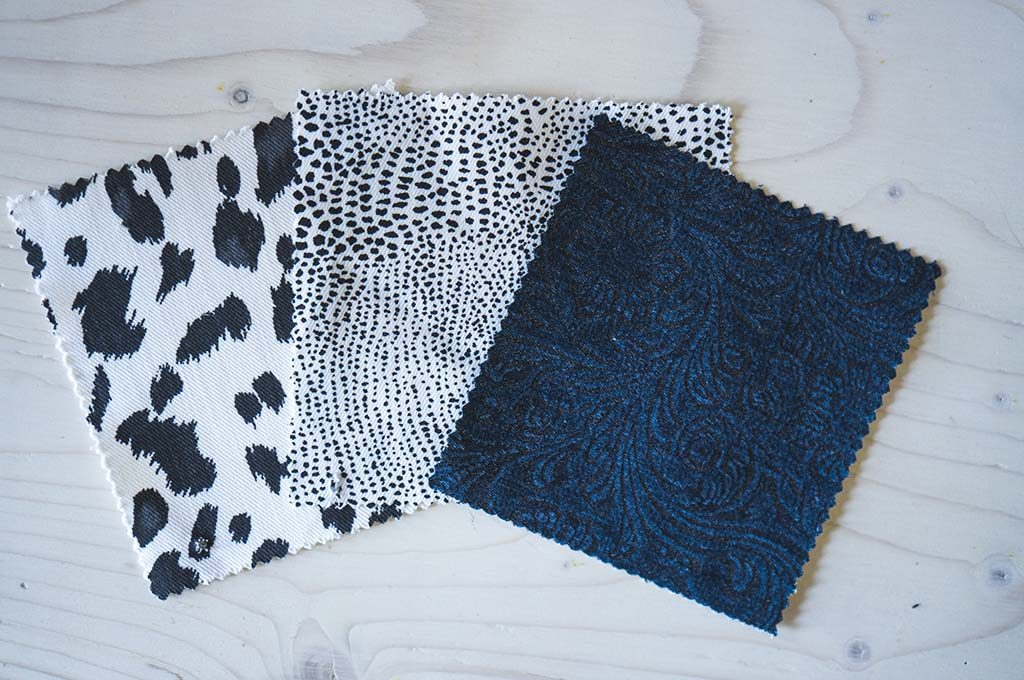
Many mills are now experimenting with new finishes and techniques to create modern, fashion-forward denim. It’s possible to source printed, waxed, foiled, and (yes, still) acid-washed denim if you’re feeling a little more daring.
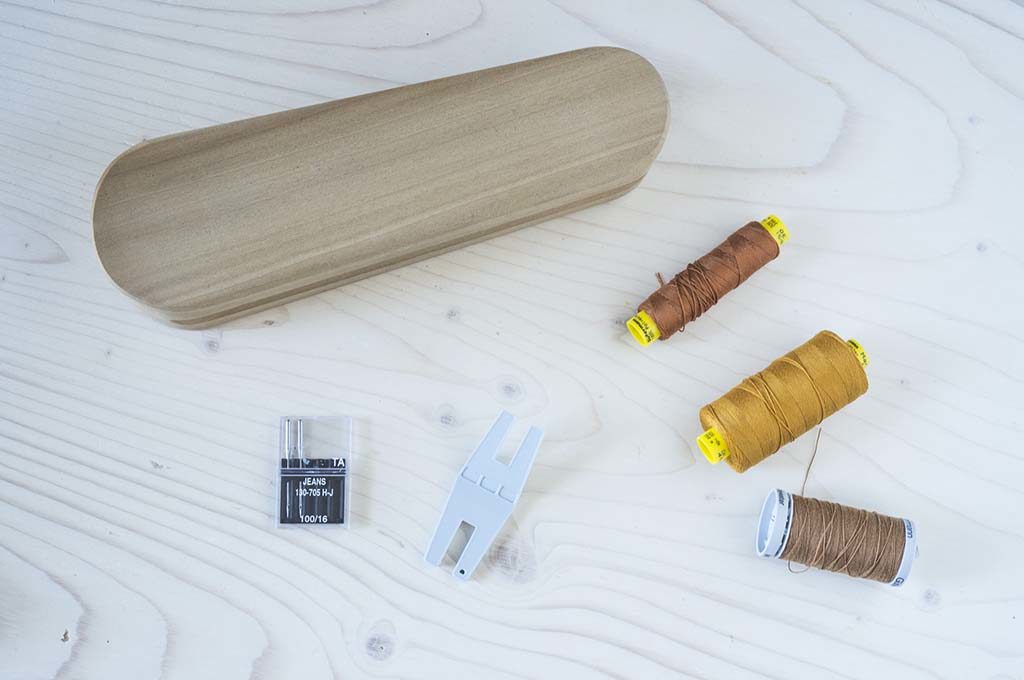
Having the correct set of tools and notions will help your denim projects run smoothly.
Heather's Tips for Sewing With Denim
- Use a needle specifically made for denim in an appropriate size. They have a strong shaft and a very sharp point and are designed to sew through multiple layers of heavy fabric.
- Cut denim on a single layer of fabric, especially when sewing jeans. Combined with alternating the direction of your leg piece, single layer cutting can help prevent leg twist.
- Press your seams with a hardwood tailors clapper. It absorbs steam and helps create strong, crisp seams even on very thick denim.
- Use a “humpjumper” or a folded piece of cardboard under your machine foot when you’re sewing over really thick denim seams. It helps keep your stitches nice and even.
- Make thick seams (especially on belt loops) thinner and easier to stitch with the judicious use of a hammer.
- Go slowly and use your handwheel over exceptionally bulky areas.
- Use an edge-stitch foot to get nice even rows of double topstitching.
- Use regular thread in your bobbin case if you’re using topstitching thread to save time when switching between threads. Test out your tension settings on a scrap of fabric before starting your project.
- Use flat fell seams for a very strong, durable seam finish for denim. If you’re having trouble folding the fabric at thick joints, increasing your seam allowance to ¾” may help you tuck everything under.
- Use rivets to help strengthen areas of high stress like pocket edges. You can apply them at home by making a hole in the fabric with an awl, and hammering the rivet into place on a hard metal surface (I like using a cast iron frying pan!) “Nipple” rivets can only be applied with a special press, so I recommend ring rivets for home use.
- Use bar tacks to not only provide support at areas of stress but also to add a little personality to your makes.
- Grade seam allowances to help reduce bulk and make it easier to sew through multiple layers of denim.
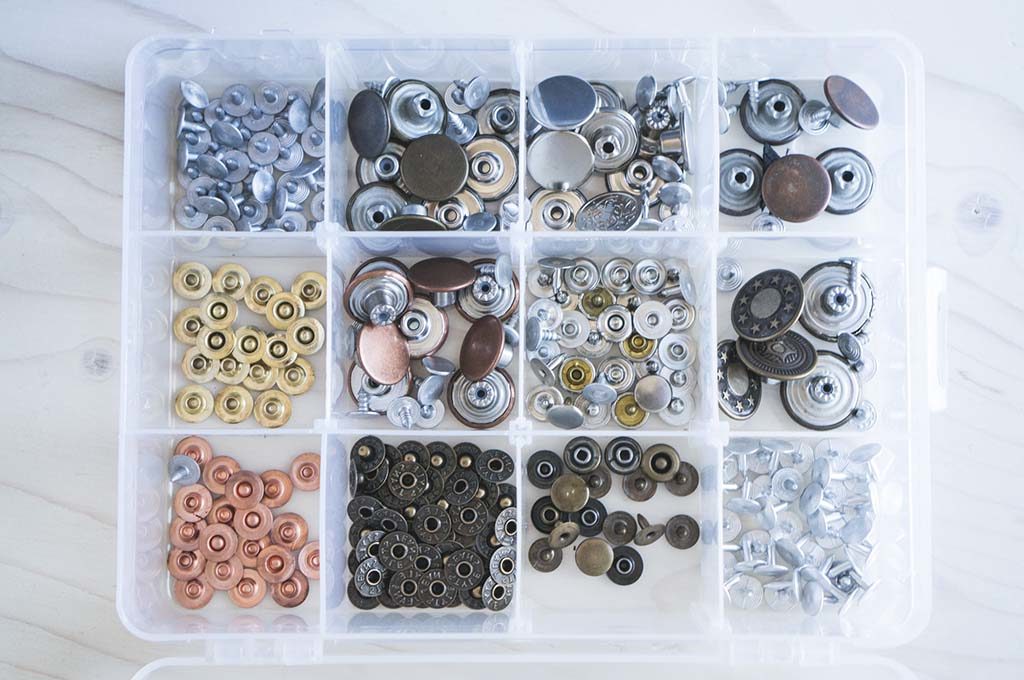
Rivets help to strengthen high stress areas on your denim projects.
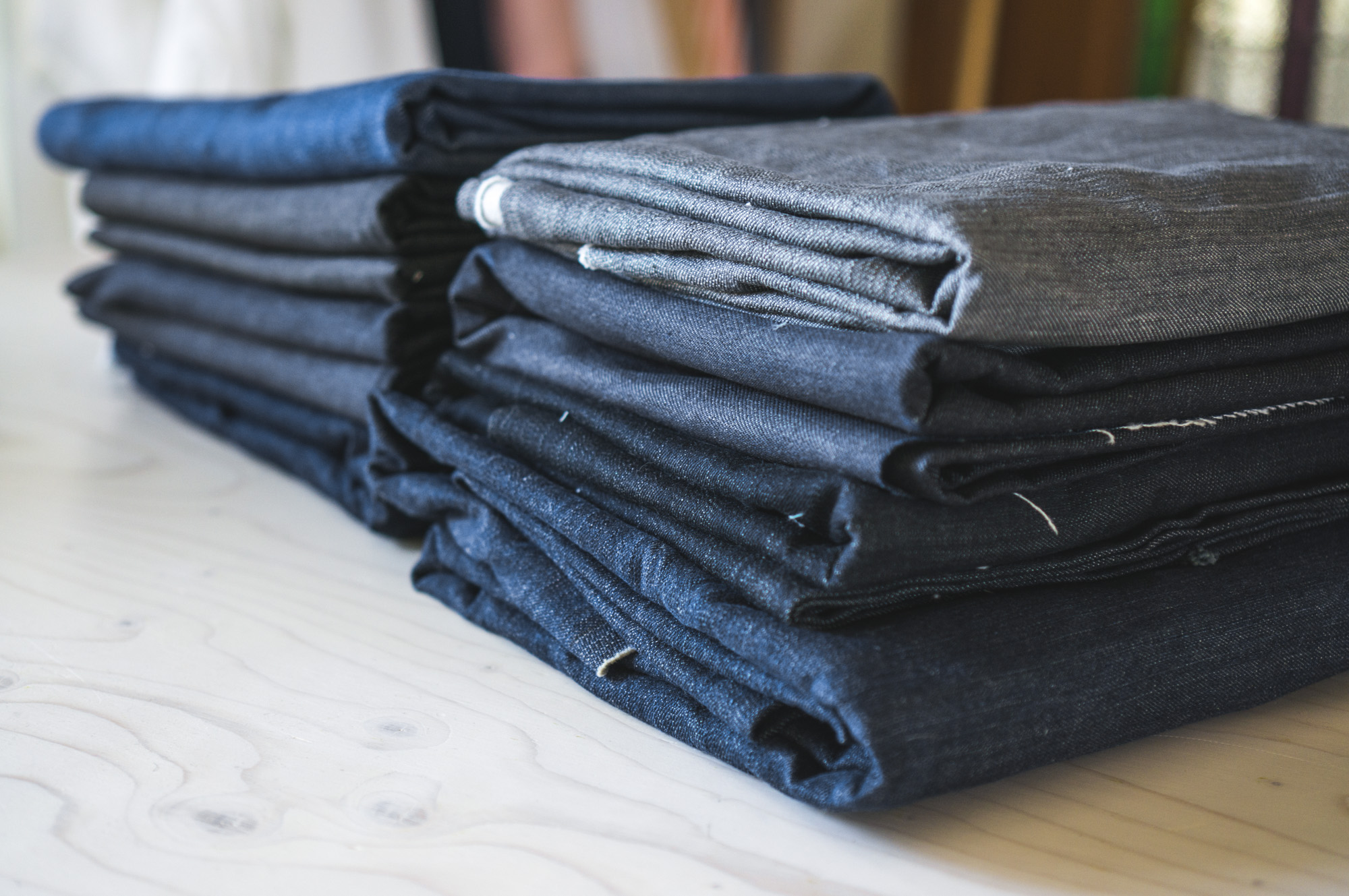
Denim Care
As with all fabrics, I always suggest pre-washing and shrinking your denim before you start to sew. This is the best practice to remove chemical sizing, soften the denim, and ensure your jeans won’t shrink on you down the road.
Wash your denim on the cold cycle with a cup of white vinegar to help preserve the dye. You can pre-shrink denim in the dryer the first time, but avoid heat with stretch denim down the road since it breaks down the Lycra. If you’d like to prevent the fabric from distorting in the wash, sew the cut ends together first to make a tube. To get as much life out of your denim makes as possible, avoid washing too frequently and steer clear of fabric softener, which is very hard on denim fibers.
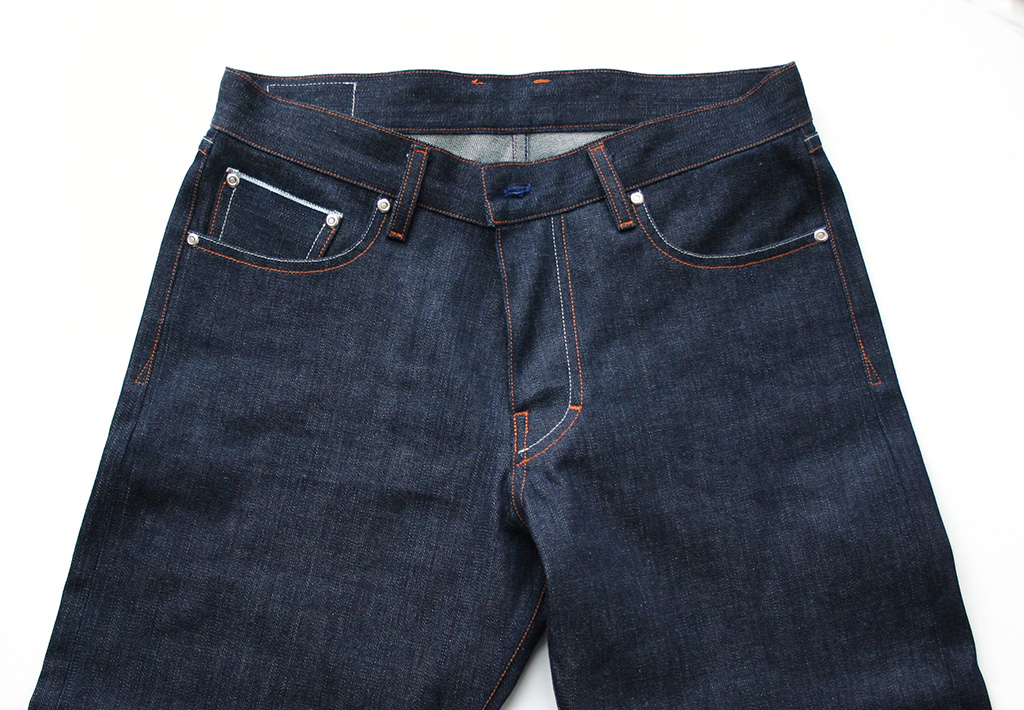
Raw denim jeans immediately after sewing. Photo Credit Taylor of Taylor Tailor.
Raw & Dry Denim
Raw denim-heads would tell you to completely ignore everything I just said. There is a popular school of denim thinking that equates washing denim with clubbing baby seals. According to this methodology, you should wear your raw, indigo jeans straight from the store, and go up to six months without washing them. This “breaking in” process fades the jeans in the areas where they get most worn – around the crotch, behind the knees, along the pockets. It creates an organic distressing that companies are otherwise artificially doing to their jeans.
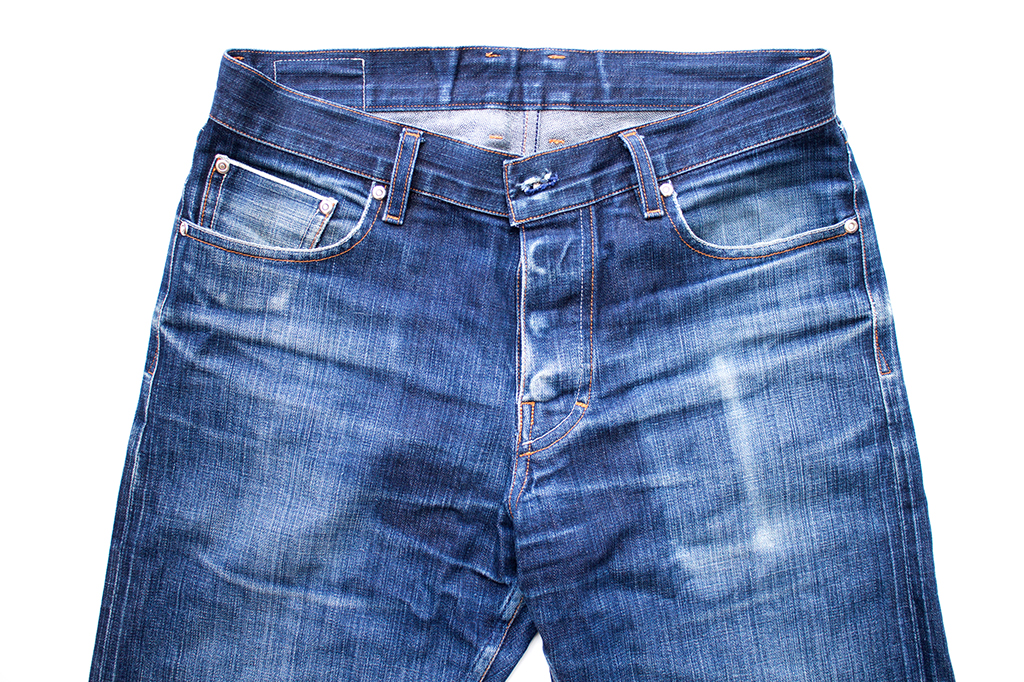
Jeans after 6 months of wear. Photo Credit Taylor of Taylor Tailor.
While you may shudder at the idea of not washing your jeans for six months, the overall effect is beautiful. As Levi Strauss said, ““Objects are what matter. Only they carry the evidence that throughout the centuries something really happened among human beings.” Your raw, faded, and worn jeans can be your story and your evidence.
If you’d like to try your hand at raw denim, make a pair of jeans with indigo denim straight off the bolt. Go as long as you possibly can without washing them, spot cleaning them or throwing them in the freezer when they need a little freshening up. When your six-month sentence is over, wash them inside out in cold water with gentle detergent to help reveal the aging process.
Where to Buy Denim
As we learned in the March issue of Seamwork Magazine, the fabric industry for sewists is frustratingly dependent on leftovers from the ready-to-wear industry. A minimum order from Cone Denim is at least 10,000 yards, making it impossible for fabric stores to order direct from the manufacturer. We are instead relying on what our fabric stores can purchase from their wholesale network, and a lot of information gets lost in the supply chain. A store may offer high-quality designer denim but cannot 100% guarantee where it was milled. Some businesses may be unaware that we’re looking for his information in the first place, so I encourage you to ask your fabric merchants about the provenance of their denim!
Resources
-
Closet Case Files: semi-annual sales for Cone Denim (sign up for the newsletter to be notified of sales.) -
Taylor Tailor: sells Cone Mills selvedge and denim notions like rivets -
Mood: Lots of designer denim. -
Girl Charlee: Some designer denim, novelty colors, and prints -
Fabric.com: This large online store carries plenty of denim in various weights. -
Emma One Sock: Great selection if high quality fabrics. -
Marcy Tilton: Carries some designer denim. -
M. Recht (Australia): A denim source in Australia. -
Ditto Fabrics (UK): Italian and Japanese denims. -
MyFabrics.co.uk (UK): Another source in the UK. -
Michael Levines http: For designer Italian denim. -
Closet Case Files Ginger Jeans sewalong: Learn to make these lovely jeans with Heather. -
Rawr Denim: Articles and information for the denim afficianado. -
Denim Dictionary: Learn all the terms in this handy guide. -
A Short History of Denim: Read more on the history of this iconic fabric.