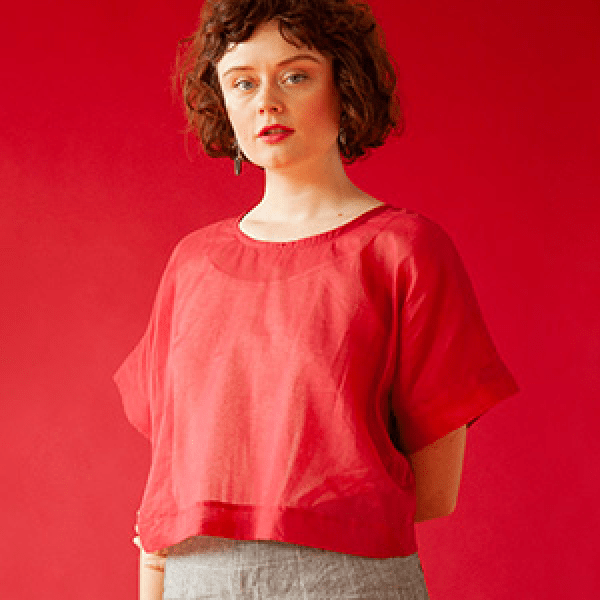
Learn to Sew a Simple Top
Start your sewing journey with this beginner-friendly online sewing class. Using the Bo pattern, you'll create a versatile woven top perfect for any fabric choice. This class combines essential sewing education with step-by-step construction guidance. You'll learn fundamental techniques like working with bias tape, creating neat sleeve cuffs, and achieving a professional finish. The Bo top's relaxed fit and simple design make it an ideal first garment project. Perfect for beginners, this class teaches lasting skills while creating a comfortable, stylish top you'll love to wear.
Non-Members: $49
Seamwork Members: Free!
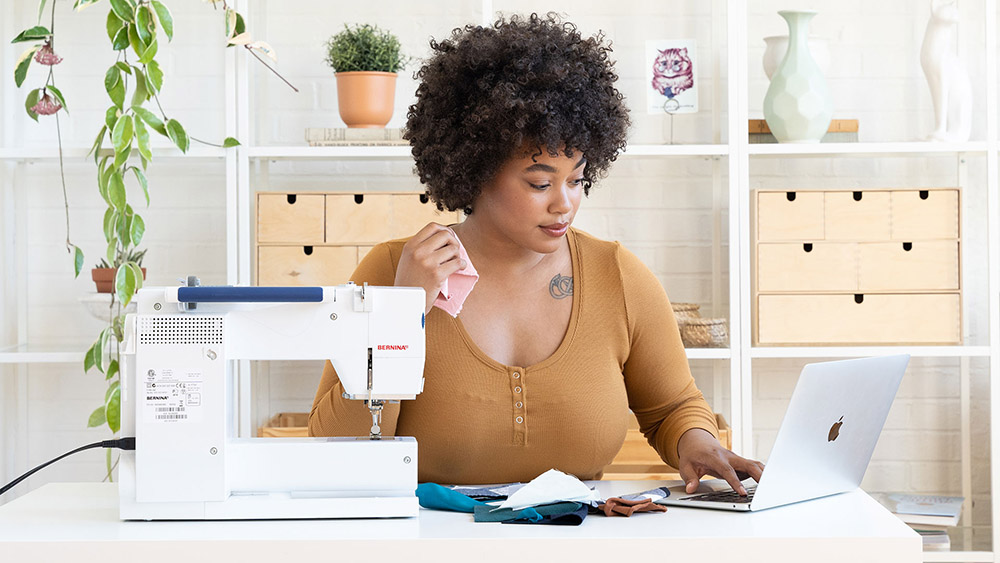
Members Only Course
Get access to this course and all other member benefits by joining Seamwork today.
Join Seamwork NowAlready a Seamwork member? Sign in here.
Join Seamwork to get full access to this Sewalong.