One of zero-waste fashion’s biggest challenges is changing the manufacturing processes that create so much waste. Small changes to large-scale manufacturing can have wide ripple effects. In this article, we’ll take a look at some of the fashion insiders who are tackling this by opening up new markets for their products, others who are inventing new technologies to solve an old problem. Either way, they’re part of a larger movement hoping to change the industry, and they’ve come up with an idea or two that we can borrow, as well.
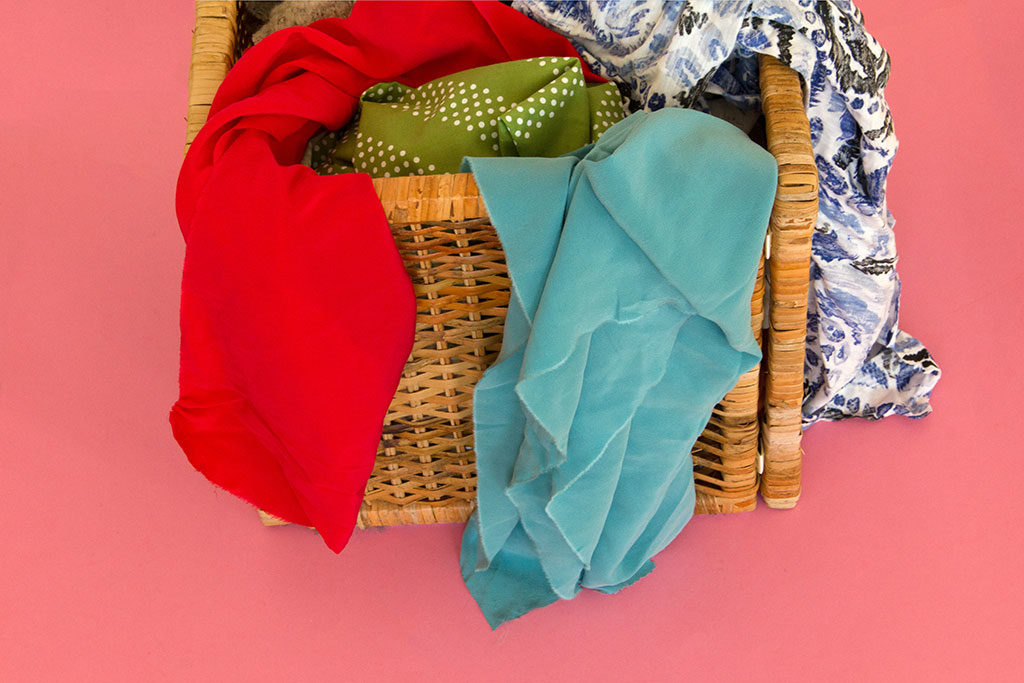
Reusing Off-Cuts
To date the most frequently used method for reducing waste generated during the manufacturing process is to take the off-cuts, or oddly-shaped bits of fabric leftover from the cutting process, and use them for other purposes. Since the garment industry wastes roughly 15% of the fabric it uses, diverting even a fraction of this waste from the landfill can really add up! Alabama Chanin, which produces cotton jersey goods for the person and the home, is a company that’s highly dedicated to eliminating waste. They’ve developed a signature appliqué look that lends itself well to incorporating off-cuts into the main garment. In addition, they sell cotton jersey pulls, which are off-cuts of leftover organic cotton jersey ties, and yarn balls, made from long ropes of jersey ties wound into balls. Potential uses include necklaces, belts, rag rugs, or just decorative display. They also sell cotton scrap bundles that can be used in quilts, appliqué, stuffing, doll clothes, animal toys, and more. MATERIALBYPRODUCT, an Australian company that specializes in silk, wool, and leather, has experimented with using off-cuts in various ways, including producing accessories (which then coordinate with the originating garment). When making a wardrobe capsule, one could easily imagine slipping a clutch or bag into the mix for additional mix-and-match possibilities.
Computer Meets Loom
What does the future of zero-waste manufacturing look like? Let’s take a quick peek at a couple promising technologies developed by eco-minded fashion insiders.
Direct Pattern on Loom
Direct Pattern on Loom (DPOL) was developed by Indian fashion designer Siddhartha Upadhyaya. Where most looms weave rectangles of fabric, DPOL connects the loom to a computer to weave fabric that is shaped as a sleeve, say, or a bodice. The resulting pieces can then be sewn together. Because no cutting is required, no waste is generated. Who knows if this technology will ever be available for the home sewist, but it’s nice to dream about tossing those pattern weights and shears, isn’t it?
A Piece of Cloth
A Piece of Cloth (A-POC) is the brainchild of Japanese fashion designer Issey Miyake, in collaboration with his colleague Dai Fujiwara. Both a manufacturing process and a label, A-POC knits fabric into tubes that are then seamed together in strategic places to create cavities; multiple garments can be woven into the fabric in this way, and once the tubes come off the loom, they are snipped open with scissors to create garments. Like DPOL, A-POC makes extensive use of technology to weave finished garments instead of fabric. The key to the A-POC process is a digital Jacquard machine—instead of using it to weave patterns, it is used to embed seams.
Wild and Wacky
Spray-on Design ©
Remember silly string? Imagine spraying a can of that onto a body or dress form, and you’ll begin to see how Fabrican Ltd.’s Spray on Fabric operates. The British company found a way to bond and liquefy fibers; once sprayed, the solvent evaporates and the fibers bond, forming a body-hugging garment. Although Spray on Fabric has been used on the catwalk, its applications are far-reaching, from health care (the fabric is sterile and can be used as a bandage) to environmental cleanup, as the fibers have the ability to absorb oil. This amazing technology boasts both zero cutting, sewing, and waste.
Tips for Using up Off-Cuts
As garment sewers we often think of using off-cuts in garments, but why not change mediums entirely? Heavier garment fabrics can work well in pillows or bags (Finch or Valencia would be excellent for using up off-cuts); linen or wool make lush home décor. A summer dress might get worn weekly, but a summer quilt will be appreciated all season long. If you’re feeling overwhelmed, here are a couple places to begin:
* Start with a favorite. Ideas tend to generate more ideas, which means just one or two off-cut projects might send countless possibilities spinning through your head. You’ll be more motivated if it’s a beloved print or color, too.